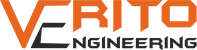
Verito Engineering offers a range of high-performance Agitators for Starch Industries, specially designed to optimize the processing and extraction of starch from various raw materials such as maize, wheat, and potatoes. Our agitators are engineered to handle the unique challenges of the starch manufacturing process, ensuring efficient mixing, superior product consistency, and energy savings across critical stages of starch production. From fiber washing to gluten separation, our agitators guarantee the highest standards of operation, making them the preferred choice for starch production facilities globally.
Key Features:
Impeller Types | Hydrofoil, Axial Flow, Radial Flow |
Material of Construction | SS304, SS316, Customizable |
Motor Power | 3 HP to 50 HP (Based on application requirements) |
Speed Control | Variable Frequency Drive (VFD) |
Viscosity Range | Suitable for medium to high-viscosity starch slurries |
Mixing Cycle Time | Process-dependent (ranges from 20-90 minutes) |
At Verito Engineering Private Limited, we understand the critical role that agitators play in the starch manufacturing process. Our Agitators for Starch Industries are meticulously designed to handle each stage of the process with precision, efficiency, and reliability. Whether it’s fiber washing, germ separation, or gluten recovery, our agitators are engineered to enhance productivity, reduce operational costs, and deliver superior product quality. Get in touch with us to learn how Verito Engineering can optimize your starch production process with our industry-leading agitators.
These mixer agitators are comes in several specifications as per the need of our customers. The offered mixer agitators are tested from our end in order to deliver a defect free range to customer's end. Our mixer agitators are developed with quality material under the direction of skilled professionals.
We ensure the highest quality & performance of our Agitators. At the same time, we have a very strong performance track record of supplying various types of agitators for various applications.