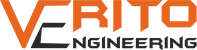
Fermentation is a critical process in industries such as pharmaceuticals, biotechnology, food & beverage, and biofuels. The Fermentation Broth Agitator is an essential component that ensures uniform mixing, optimal aeration, and efficient mass transfer, leading to enhanced microbial and enzymatic activity.
At Verito Engineering Private Limited, we offer cutting-edge Fermentation Broth Agitators designed to optimize process performance, from lab-scale development to full-scale production. Our solutions are tailored to meet the most stringent industry standards, ensuring high efficiency, energy savings, and regulatory compliance.
Engineering & Development Support
During this phase, process feasibility is assessed, and initial design concepts are developed. Verito Engineering supports customers by:
Manufacturing, Installation & Optimization
In this phase, agitators are manufactured, installed, and optimized for peak performance. Verito Engineering ensures:
Key Features
Parameter | Specification |
Drive Type | Top-entry |
Motor Power | 0.5 kW to 75 kW (customizable) |
Speed Range | 10 - 500 RPM (VSD available) |
Material of Construction | SS304L, SS316L, SS904L, Alloy 926 |
Seal Type | Single/Dual Mechanical Seal or Lip Seal |
Impeller Types | Rushton, Concave, Hydrofoil, Pitched Blade |
Sterilization Compatibility | CIP/SIP Ready |
Mounting Options | Flange Mounted |
For customized solutions, contact Verito Engineering Private Limited today and optimize your fermentation processes with our high-performance Fermentation Broth Agitators.
These mixer agitators are comes in several specifications as per the need of our customers. The offered mixer agitators are tested from our end in order to deliver a defect free range to customer's end. Our mixer agitators are developed with quality material under the direction of skilled professionals.
We ensure the highest quality & performance of our Agitators. At the same time, we have a very strong performance track record of supplying various types of agitators for various applications.