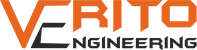
At Verito, we pride ourselves on being at the forefront of engineering excellence, delivering high-performance Flue Gas Desulfurization (FGD) agitators that stand as a benchmark in the industry. Our commitment to quality, innovation, and environmental sustainability drives us to create agitators that not only meet but exceed the rigorous demands of modern industrial processes.
Understanding the FGD Challenge
Flue Gas Desulfurization (FGD) is a critical process in reducing sulfur dioxide (SO₂) emissions from industrial exhaust gases, particularly in power plants and large-scale industrial operations. The agitator is a vital component in this process, ensuring the effective mixing of slurries to maximize the contact between the flue gas and the absorbent, leading to efficient SO₂ removal.
Verito: Your FGD Agitation Partner
Verito is a global leader in designing and manufacturing cutting-edge agitator solutions specifically tailored for FGD applications.
Our FGD agitators are specifically designed to handle the unique challenges presented by different types of desulfurization systems, including limestone, gypsum, magnesium oxide, and ammonia-based FGD processes. A key feature of our agitators is the use of Alloy 926 or higher-grade materials in impeller construction, ensuring exceptional resistance to corrosion and wear in aggressive environments. Here’s a detailed look at how Verito agitators enhance each critical aspect of the FGD system:
Absorber Agitators
Limestone Slurry Preparation and Storage
Absorber Drain Tank
Reclaim Water/Reuse Water Tanks
Gypsum Slurry
Area Sumps and Wastewater Treatment
Chloride Bleed Wastewater Treatment / Heavy Metals Removal
Fly Ash Make-Down and Storage
Motor Power | Upto 100 kW |
% Solid Concentration | 0-70% (W/W) |
Impeller Diameter | 300mm – 4000mm |
Shaft Diameter | 30-300 mm |
Impeller Type | Hydrofoil, Wide Foil, Turbine |
Materials (Wetted Parts) | EN8+RL, EN24+RL, Alloy 926 or Better Grade |
Customization and Engineering Excellence
Verito’s commitment to customer satisfaction is reflected in our ability to provide tailored solutions. Our engineering team employs advanced design tools and simulation software to optimize agitator performance for specific FGD applications.
Benefits of Verito Agitation Solutions
For more information on how Verito’s FGD agitators can enhance your operations, contact our team today. We are dedicated to providing solutions that are as unique as your process needs.
These mixer agitators are comes in several specifications as per the need of our customers. The offered mixer agitators are tested from our end in order to deliver a defect free range to customer's end. Our mixer agitators are developed with quality material under the direction of skilled professionals.
We ensure the highest quality & performance of our Agitators. At the same time, we have a very strong performance track record of supplying various types of agitators for various applications.