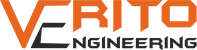
At Verito Engineering Private Limited, we specialize in designing high-performance agitators for Water Treatment Dosing Tanks, engineered to meet the complex demands of various water treatment processes, including Water Treatment Plants (WTP), Wastewater Treatment Plants (WWTP), Sewage Treatment Plants (STP), Effluent Treatment Plants (ETP), and Desalination projects. Our agitators ensure the effective mixing of chemicals and slurries to maintain precise dosing levels for optimal water quality.
Key Features and Benefits
Applications in Food Processing
Advantages of Verito Engineering Agitators
Motor Power | 0.5 HP to 25 HP, based on tank volume and viscosity |
Speed Range | Variable speed control from 0 to 1500 RPM |
Mixer Shaft Length | Customizable from 500 mm to 8000 mm, depending on tank depth |
Impeller Diameter | 200 mm to 4500 mm, based on application |
Impeller Types | Hydrofoil, Pitched Blade, Propeller, Anchor |
Material of Construction | SS304, SS316, Alloy 926, Hastelloy, with optional lining (FRP, Rubber, PP, HDPE, PVDF, PFA, PTFE) |
Mounting Type | Top entry, adjustable brackets |
Power Supply | Single-phase and three-phase |
Operating Voltage | 230V for single-phase, 415V for three-phase |
Seal Type | High-quality seals for chemical and fluid containment |
Compliance | ATEX-rated options available for explosive atmospheres |
Applications | Poly, Lime, Alum, SMBS, Antiscalants, Coagulants, Anoxic Tanks, Sludge Treatment |
At Verito Engineering Private Limited, we understand the critical role that agitators play in the efficient operation of water treatment processes. Whether in WTP, WWTP, STP, ETP, or desalination applications, our agitators ensure reliable and consistent mixing of dosing chemicals, leading to enhanced plant performance and reduced operational costs. With customizable designs, energy-efficient solutions, and superior material construction, we deliver agitators that meet the rigorous demands of modern water treatment facilities.
For more information or to request a custom solution for your water treatment plant, contact Verito Engineering Private Limited today. Let us help you optimize your water treatment process with our advanced mixing technology.
These mixer agitators are comes in several specifications as per the need of our customers. The offered mixer agitators are tested from our end in order to deliver a defect free range to customer's end. Our mixer agitators are developed with quality material under the direction of skilled professionals.
We ensure the highest quality & performance of our Agitators. At the same time, we have a very strong performance track record of supplying various types of agitators for various applications.